当社は、創業から150年以上の歴史があり、スピンドル製造を通して培ったコア技術を活かし、繊維機械向けのスピンドルを始めとして、小型の精密加工部品、工作機械向けのスピンドルなど、新たな分野への展開を進めて参りました。
近年では、機器メーカーとのタイアップにより、当社のモータースピンドルを用いて赤色半導体レーザーをワーク内壁に照射する事でワーク内壁の傷やバリの有無を自動検出する、量産現場で活用可能な検査装置の販売をさせて頂いております。
当社の検査装置のメリット
- 検査工程の自動化により、検査コストが削減出来ます。
- 不良品の流出を防止出来ます。
- トレーサビリティが向上します。
- 検査品質の個人差を解消出来ます。
特徴
- 非破壊、非接触で、目視では行き届かない箇所の検査が出来ます。
- 欠陥の判定基準を設定する事で、OK/NG判定を自動化できます。
検査対象部品
バルブボディ、マスターシリンダー、シリンダーブロック、スリーブ、ミッションケース、インバーターケース、コンバータケース、ハウジング、ピストンなど
対象箇所
内径表面、ネジ穴など
欠陥種類
巣穴、傷、バリ、欠け、切粉、切削痕、びびり、剥離、打痕、未加工など
対象材質
アルミニウム、ステンレス、鉄、銅、チタン、セラミック、樹脂、プラスチックなど
欠陥検出したいサンプルワークをご準備頂ければ、サンプルテストは無償で対応させて頂きます。穴ライザーで欠陥検出が可能かサンプルテストを実施し、結果を報告書にまとめて提出させて頂きます。お気軽にお問合せください。
今後の展開
従来は穴の傷などの欠陥検査のみでしたが、現在は欠陥検査に加え、内径、真円度を同時測定出来る検査測定装置も販売しております。
また、ベアリングの鋼球などの外径の傷を自動検査する「球体検査装置」も開発致しました。今後も新たな用途、要素に対しての技術革新を進めて参ります。
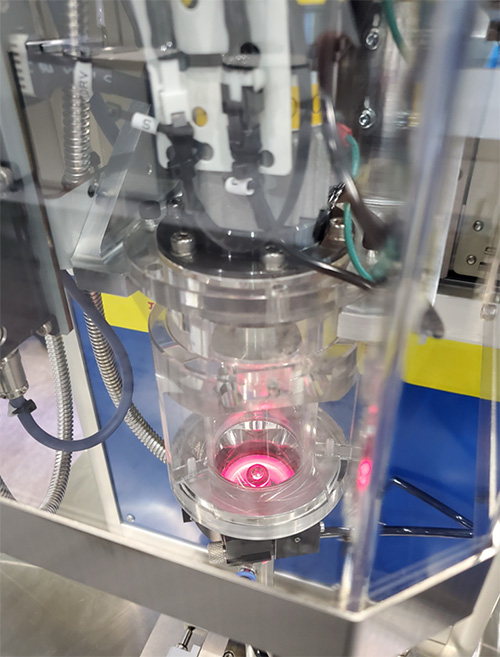